成形刀具畢業設計開題報告精選
論文堡
日期:2023-11-20 17:09:09
點擊:425
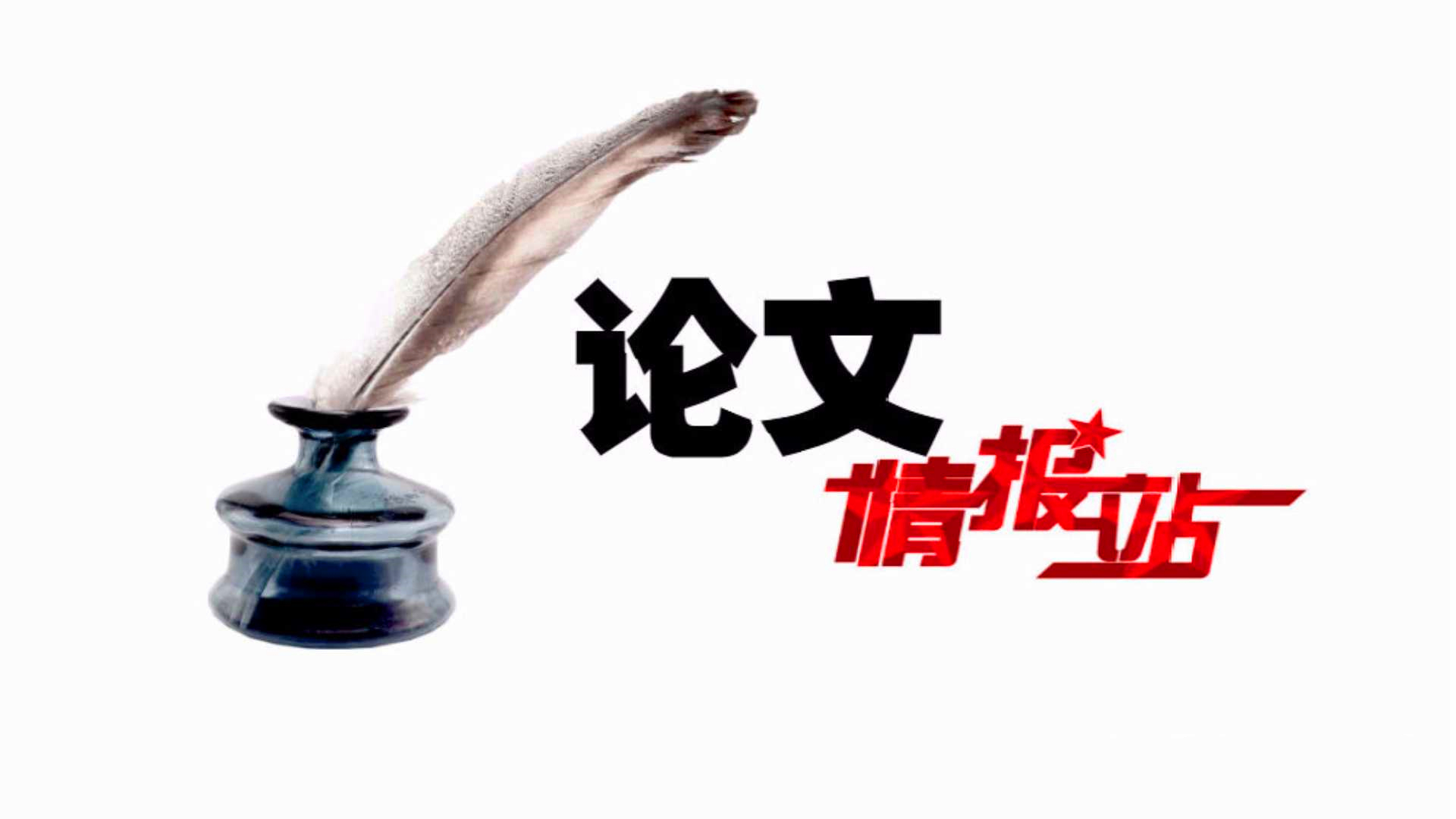
本文是一篇開題報告,參考文獻是在學術研究過程中,對某一著作或論文的整體的參考或借鑒。征引過的文獻在注釋中已注明,不再出現于文后參考文獻中。(以上內容來自百度百科)今天論文堡為大家推薦一篇開題報告,供大家參考。
一、數控漸進成形技術介紹
學者schmoeckel在他的著作中預言隨著自動控制技術的不斷發展進步,板料成形設備將會變得更加靈活。leszak在其申請的專利中首次提出了利用簡單成形工具對板件進行加工的板料無模成形思想,但受限于當時的技術水平這種技術沒有進一步向前發展。后來隨著相關技術的不斷發展,直到上個世紀90年代,松原才正式提出了板料數控漸進成形技術。
板料數控漸進成形技術引入“分層制造”的思想,首先將要加工的零件在高度上離散成若干層,再由cad/cam軟件在每層沿零件輪廓生成相應的加工軌跡,簡單的成形工具頭沿著該軌跡對板件進行逐層加工,得要想要加工的零件。由于數控漸進成形是對板料進行逐層逐點進行加工,靠局部變形的積累獲得整個零件,因此具有加工方式靈活、加工精度高等優點,能夠成形出形狀復雜的鈑金零件。數控漸進成形技術從零件的三維結構設計到零件的加工軌跡生成再到零件最終成形都具有很強的靈活性,零件的尺寸或者形狀變動時只需在cad/cam軟件里改動零件模型即可。因此,該技術特別適合用于鈑金類新產品的開發、試制及小批量生產。
板料數控漸進成形技術按其加工方式分為單點(負)漸進成形和雙點(正)漸進成形。單點漸進成(single point incremental forming-spif)是一種不需要任何模具支撐的漸進成形方式。金屬板被夾具固定在支架上,板下面懸空,工具頭沿特定的軌跡由金屬板四周向中心逐漸加工,此時金屬板在力的拉伸作用下變形。零件成形過程中金屬板料只跟工具頭接觸,成形過程中不需要模具支撐,因此單點漸進成形具有加工方式靈活、加工范圍廣、對設備依賴性不強、占用生產資源少等特點。此外,只需要在cad軟件里改變零件幾何模型就可以獲得不同的成形軌跡,進而加工出相應形狀的零件,所以單點漸進成形的操作性較好,但是因為成形過程中只是工具頭和金屬板的接觸,系統剛度相對較小,成形后零件容易發生回彈,導致零件成形精度較差。
二、數控漸進成形優缺點
不同與沖壓等塑性加工工藝,數控漸進成形是金屬板件塑性加工的一種新的成形方式,主要有以下優點:
1.無模加工
漸進成形不需要專門的成形模具即可對金屬板進行加工,特別是單點漸進成形技術,真正實現了無模具加工;即使是雙點漸進成形也僅僅需要簡單的模具,而且模具的制作可以是代木、纖維等材料,相對于沖壓模的制作能大大節省時間成本和資金成本。
2.成形設備簡單、成本低
漸進成形技術對設備的依賴性不高,普通的數控銑床進行簡單的改造后就可以達到專用漸進成形機床的加工效果,對板料的漸進成形可以在普通數控銑床、漸進成形專用機床、數控加工中心等設備上實現;用來進行漸進成形刀具只是簡單的圓形成形工具頭,工具頭不需要特殊的加工處理,只需保證硬度和表面粗糙度即可,這也降低了加工成本。
3.適合新產品的開發
市場上常見的商用cad/cam軟件里就可實現從零件結構設計到加工參數優化再到成形軌跡生成整個過程的無縫銜接;當零件尺寸需要改動時,只需在軟件中改動相應的結構模型就可以實現成形軌跡的改變。
4.復雜板料零件成形
由于漸進成形是對板料進行逐點逐層成形因此可實現對復雜鈑金類零件的成形且成形精度高。
5.成形力小
零件漸進成形過程中只有工具頭底部很小的區域與板料相接觸,每層板料變形區域也僅限于該區域,且工具頭在相鄰加工層之間的進給量δz一般為0.2mm-1mm,因此所受成形力較小。
6.成形過程無噪音污染,對環境友好
零件漸進成形時,特別是進行單點漸進加工時,金屬板和工具頭的接觸區域很小,加工過程中不會出現振動、沖擊等現象,整個加工過程中幾乎無噪聲污染。
三、數控漸進成形研究現狀
板料數控漸進成形技術是在現代社會消費者對產品多樣化、個性化需求越來越多的背景下提出的,是一種新型的適合新產品開發、試制的制造技術,該技術的進一步發展不僅可以豐富塑性加工理論的知識體系,還具有廣闊的工業應用空間。數控漸進成形技術自被提出以來,便憑借自身的優點引起國內外大量學者的廣泛關注。目前,對該技術的研究主要集中在下幾個方面:
成形極限圖(flc)通常用來描述一種工藝的成形性能。大量研究表明漸進成形技術的成形極限圖大致是一條位于第一象限負斜率的直線,而傳統的成形極限圖是一條v線,如圖1.6所示。因此,漸進成形技術能顯著提升材料的加工潛力,成形出大應變的零件。hagan和jeswiet對比研究了旋轉成形、旋壓成形和漸進成形三種板料成形技術的成形特征和成形機理,凸顯了板料漸進成形技術的優勢。jackson和allwood對拼焊銅板進行了漸進成形,研究零件成形過程中金屬板的變形過程和變形機理。作者分別測量了單點漸進成形和雙點漸進成形后零件厚度方向上的應變分布,發現在與工具頭運動方向相切的方向上,板料主要發生拉伸和剪切變形,與在工具頭運動平行的方向上,板料主要發生剪切變形;作者還發現隨著拉伸和剪切作用的不斷加劇,零件實際測量厚度跟正弦曲線預測厚度之間的誤差會逐漸增大。s. gatea等研究了主要成形參數對板件成形性能的影響,發現零件經多道次漸進成形后壁厚分布更均勻;增量步長對板件成形性能的影響還不十分明確;增加主軸轉速或者減小工具頭進給速度都能使板件成形性能提高;小尺寸圓形工具頭螺旋軌跡加工時,板件極限成形角較大。c.raju等將幾個薄銅板疊加在一起進行單點漸進成形,分別得到每塊薄銅板的成形極限圖,研究每塊薄銅板的成形性能。
劉兆兵等通過試驗驗證了板料的成形性能跟成形角度和刀具軌跡的垂直進給量有關,作者還研究了不同成形參數對工具頭與金屬板之間成形力的影響。馬琳偉等數值模擬不同成形軌跡下零件漸進成形過程,作者將零件分成四個不同的變形區,探討每個變形區的變形特點和變形過程。
四、提綱
致謝
摘要
abstract
第一章
1.1 引言
1.2 數控漸進成形技術
1.2.1 數控漸進成形技術介紹
1.2.2 數控漸進成形基本流程
1.2.3 數控漸進成形重要幾何參數
1.3 數控漸進成形優缺點
1.3.1 數控漸進成形的優點
1.3.2 數控漸進成形的缺點
1.4 數控漸進成形研究現狀
1.5 課題目的和主要內容
1.5.1 課題研究的目的
1.5.2 課題研究的主要內容
1.6 本章小結
第二章 曲面零件單點漸進成形質量及成形機理分析
2.1 引言
2.2 曲面零件單點漸進成形缺陷分析
2.2.1 表面壓痕
2.2.2 平緩曲面處成形質量和垂直尺寸精度
2.2.3 成形時間
2.3 單點漸進成形機理分析
2.3.1 單點漸進成形應力狀態
2.3.2 單點漸進成形應變狀態分析
2.3.3 單點漸進成形零件厚度
2.4 本章小結
第三章 單點漸進成形有限元模型的建立
3.1 引言
3.2 單點漸進成形的有限元模型
3.2.1 實體模型
3.2.2 單元的選擇
3.2.3 材料模型
3.2.4 網格劃分
3.2.5 摩擦和接觸
3.3 成形軌跡
3.3.1 工具頭運動軌跡設計原則
3.3.2 軌跡生成和加載
3.4 本章小結
第四章 曲面零件單點漸進成形刀具軌跡優化(一)
4.1 引言
4.2 基于增量角度 δθ 的優化方法
4.3 試驗驗證
4.3.1 零件模型
4.3.2 試驗設備和材料
4.3.3 試驗方案
4.4 試驗結果及分析
4.4.1 表面痕跡
4.4.2 零件平緩表面處成形質量和垂直尺寸精度
4.4.3 成形時間
4.5 有限元數值模擬
4.5.1 零件厚度
4.5.2 等效塑性應變
4.5.3 等效應力
4.5.4 尺寸精度
4.6 斜壁零件成形試驗
4.6.1 試驗方案
4.6.2 成形精度
4.6.3 零件厚度
4.6.4 成形時間
4.7 本章小結
第五章 曲面零件單點漸進成形刀具軌跡優化(二)
5.1 引言
5.2 基于增量弧長s_0的優化方案
5.3 試驗驗證
5.3.1 試驗方案
5.4 試驗結果及分析
5.4.1 表面痕跡
5.4.2 零件平緩表面處成形質量和垂直尺寸精度
5.4.3 成形時間
5.5 有限元數值模擬
5.5.1 零件厚度
5.5.2 等效塑性應變
5.5.3 等效應力
5.5.4 尺寸精度
5.6 兩種優化方法的對比
5.6.1 操作性
5.6.2 試驗效果
5.7 另外一種曲面零件成形實例
5.8 本章小結
第六章 總結與展望
6.1 總結
6.2 展望
參考文獻
五、課題目的和主要內容
課題研究的目的數控漸進成形技術早在上世紀90年代就被有關學者提出,但至今為止仍沒有大規模的應用于工業生產中,成形質量缺陷是制約該技術發展的重要因素,因此提高零件單點漸進加工質量是國內外學者研究的重點。本課題首先旨在總結歸納曲面零件單點漸進成形質量缺陷及其原因。其次,提出改善曲面零件單點漸進成形表面質量的一般性方法并通過試驗驗證。最后,運用有限元數值模擬,對比分析不同工藝參數對曲面零件單點漸進成形性能的影響,為實際加工時參數的選擇提供參考。
本課題針對變角度曲面零件漸進成形后表面質量差的問題,主要做了以下幾項工作:
1)總結歸納曲面零件單點漸進成形質量缺陷及其原因。
2)提出一種基于零件截面曲線形狀用增量角度dθ來控制增量步長dz的方法,建立增量步長dz與增量角度dθ之間的計算關系,并將此方法成功應用于變角度曲面零件成形,通過試驗對比該方法與傳統加工方法在零件表面壓痕、平緩曲面處成形質量、成形尺寸誤差、成形時間等方面的區別;使用該方法加工斜壁零件,在零件厚度、零件尺寸精度、加工時間等方面與固定增量步長成形方法做對比。
3)提出一種基于零件截面曲線形狀用增量弧長s0來控制增量步長dz的方法,建立增量步長dz與增量弧長s0之間的計算關系,以變角度曲面零件為例試驗驗證該方法的可行性,試驗對比研究該方法與傳統加工方法在零件表面壓痕、平緩曲面處成形質量、成形尺寸誤差、成形時間等方面的區別。
4)使用ansys/workbench有限元軟件數值模擬曲面零件漸進成形過程,分別模擬不同增量步長δz、不同增量角度δθ和不同增量弧長s0時的曲面零件成形過程,對比分析不同成形方法成形過程中金屬板塑性應變、零件成形厚度、零件成形精度等方面的差別。
六、進度安排
20xx年11月01日-11月07日 論文選題、
20xx年11月08日-11月20日 初步收集畢業論文相關材料,填寫《任務書》
20xx年11月26日-11月30日 進一步熟悉畢業論文資料,撰寫開題報告
20xx年12月10日-12月19日 確定并上交開題報告
20xx年01月04日-02月15日 完成畢業論文初稿,上交指導老師
20xx年02月16日-02月20日 完成論文修改工作
20xx年02月21日-03月20日 定稿、打印、裝訂
20xx年03月21日-04月10日 論文答辯
七、參考文獻
[1]e. quigley, j. monaghan .metal forming:an analysis of spinning processes, journal ofmaterials processing technology.2000, 103(1): 114-119.
[2]kang d c, gao x c, meng x f, et al. study on the deformation mode of conventionalspinning of plates[j]. journal of materials processing technology, 1999, 91(1-3):226-230.
[3]jurisevic b, kuzman k. water jetting technology: an alternative in incremental sheet metalforming[j]. the international journal of advanced manufacturing technology, 2006,31(1):18-23.
[4]李明哲,陳建軍,隋振,等。板材三維曲面多點成形技術[j].新技術新工藝,2000(10):27-29.
[5]li m, liu y, su s, et al. multi-point forming: a flexible manufacturing method for a 3-dsurface sheet[j]. journal of materials processing technology, 1999, 87(1–3):277-280.
[6]park j j, kim y h. fundamental studies on the incremental sheet metal forming technique[j].
journal of materials processing technology, 2003, 140(1–3):447-453.
[7]schmoeckel d. developments in automation, flexibilization and control of formingmachinery[j]. cirp annals - manufacturing technology, 1991, 40(2):615-622.
[8]leszak e. apparatus and process for incremental dieless forming: us, us 3342051 a[p].1967.
[9]松原茂夫。數值控制逐次成形法。塑性と加工。1994(11):1258-1263.
[10] hagan e, jeswiet j. a review of conventional and modern single-point sheet metal formingmethods[j]. proceedings of the institution of mechanical engineers part b journal ofengineering manufacture, 2003, 217(2):213-225.
相關文章
人力資源新增
人力資源熱點